Norwood Yarn: From Sheep to Hat
2023 UPDATE: In the 7 years since this post was written we've continued to work with Pine Hollow Farm and Wellington Fibres to produce an annual batch of Norwood yarn, as well as our Elora gradient sets. We've gradually increased the amount we produce over the years to keep up with demand, as our customers have discovered what a wonderful yarn this is to work with.This year we're up to 75lbs of raw fleece, more than triple our original order! The past few years we haven't washed the fleece ourselves (due to COVID and Debbie's maternity leave it's made more sense to send it straight to the mill to be fully processed there) but we're grateful to have had the experience of working with the raw fibre first-hand in previous years.
The story of our Norwood yarn started last winter, as Elizabeth and I discussed the idea of adding a new Canadian-grown 100% wool yarn to our products. We really wanted to pursue the idea of adding more locally-sourced yarn, and we knew that we needed to have a plan in place before shearing season if we wanted to move forward with it this year.
The first step was to find a source of high-quality fleece. We don't happen to know many sheep farmers, so we got in touch with Donna Hancock from Wellington Fibres, where we'd had our Cambiata yarn spun in the past. Donna very kindly put me in touch with Allison of Pine Hollow Farm near Norwood Ontario, and we made arrangements to get samples of some of her fleece. Allison calls the fleece from her flock "Norbouillet" as it is a Rambouillet cross that she has been breeding for so many years that it is now specific to her farm.
The fleece samples were lovely, even softer than some of the imported Merino we've worked with, so we went ahead and bought 20lbs of raw fleece. The fleeces we received were from eight different sheep (Yoshana, Xavier, Ziera, Zeeta, Xutoo, Tierney, Thekla, and Yoki) several of whom were prize-winners at the Norwood Fair and the Royal Winter Fair.
20 lbs is a lot of fleece! I picked it up from the post office in a giant canvas mailbag.
The next step in this sheepy adventure was to wash the fleeces.
It came out of the mailbag and went directly into mesh laundry bags, to keep it tidy while we washed it.
From there it went into a 20 minute soak in very hot water. I know some people will add boiling water at this stage to get the soaking bath hot enough, but we were lucky that the tap water at our studio was hot enough without that step. At first I tried using laundry detergent in the water, but I decided I didn't like the scent and ended up using the textile detergent I normally use to rinse after dyeing. It worked just fine, and kept the wool smelling like sheep, rather than a combination of sheep and "spring breeze"...
It's pretty amazing how the raw fleece almost melts into the hot water as the lanolin begins to dissolve. The water became brown instantly, so we knew we were getting all the dirt and grease out!
Each bag of fleece went through two more plain hot water rinses after the initial bath with detergent. Since we had so much of it to get through we set up a production line. The process took Elizabeth and I most of an afternoon - Henry helped us out by napping while we worked.
After each bag had been through it's final rinse, we put it in our amazing spin-dryer machine to remove as much moisture as possible and make the drying time faster.
We started out trying to fit all the fleece onto our drying rack, rigged with some of our drapery cloths that we use for shows. We soon ran out of room though, and I realised that this was a part of the process I hadn't completely thought through. Where were we going to dry 20lbs of fleece?!
Everywhere, it turns out! At the end of the afternoon we spread out a cloth, and pretty much covered the entire floor of our little studio.
We left it over night, I went back the next day to turn it and make sure it dried evenly and within another day it was dry enough to pack up and send to Wellington Fibres to be spun into yarn.
Henry helped out again, with weighing the clean fibre and packing it up to ship off.
Out of the original giant bag of fleece we ended up with about 14 lbs of clean fibre. It lost a bit more weight on it's trip through the mill, and came back as beautifully soft DK weight 3-ply yarn, weighing just under 12 lbs. This time the box fit on the back of my bike!
The next step was to try dyeing it. I like to do small sample skeins when trying out colours for a new yarn. Then Elizabeth and I discuss which ones we like, and I multiply the recipe for a larger batch.
The last step, after the chosen colours were dyed, was to get our photographer (the talented Tudor Parau) into the studio to take some photos, and get the final product up for sale on our website.
After all that, I was itching to get my hands on this yarn and actually knit something with it! We needed a new sample for our Winter Sonata pattern, so I took the opportunity to knit one in the Pirate Cove colourway with Natural as the contrast.
Leave a comment
Also in News
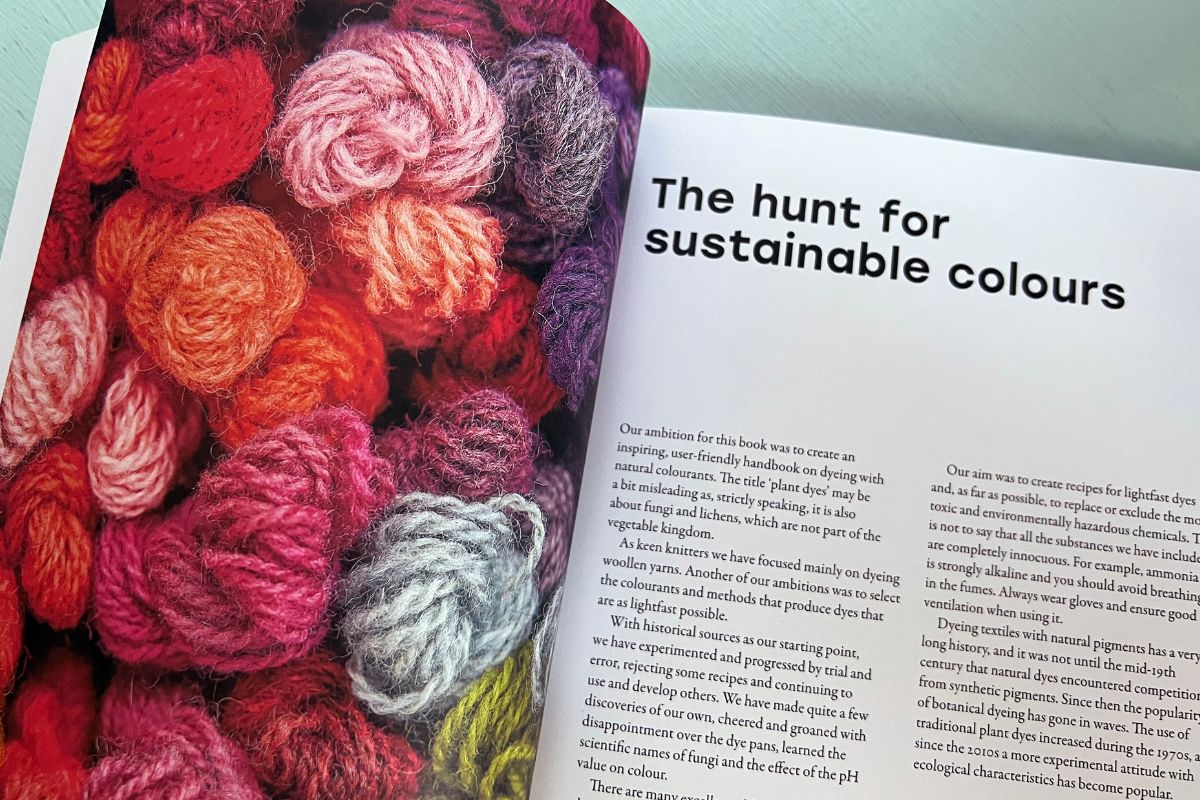
Choosing a Natural Dye Book
Have you ever tried dyeing your own yarn using natural colorants? Are you now looking for more inspiration? Or maybe you’ve always been curious, and are wondering where to begin. Below, we’ve introduced four books that could be exactly what you’re looking for!

Knitting Comfortably: The Ergonomics of Handknitting
One month ago, I found myself in the emergency room with unbearable back pain. I later learned it was caused by a herniated disc and osteoarthritis (OA) that had taken over my entire lower back. Would I ever be able to dye yarn again, let alone... knit...?
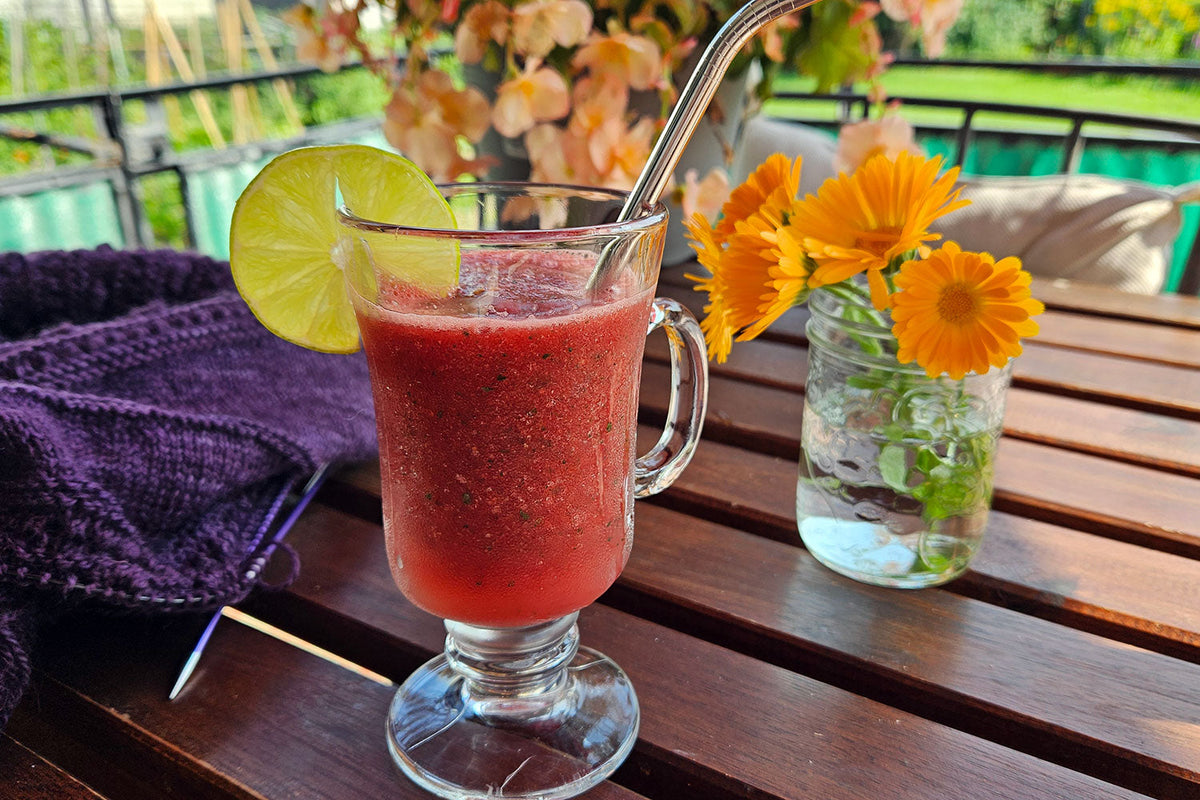
Recipe: Watermelon Slushie
What do you do when you have a glut of watermelon? Freeze it and make watermelon slushie! I started doing this last summer and it's the perfect way to use up a watermelon, especially one that's a bit overripe. Plus, with a touch of lime and mint it really hits the spot on a hot day!
Debbie Sullivan
Author